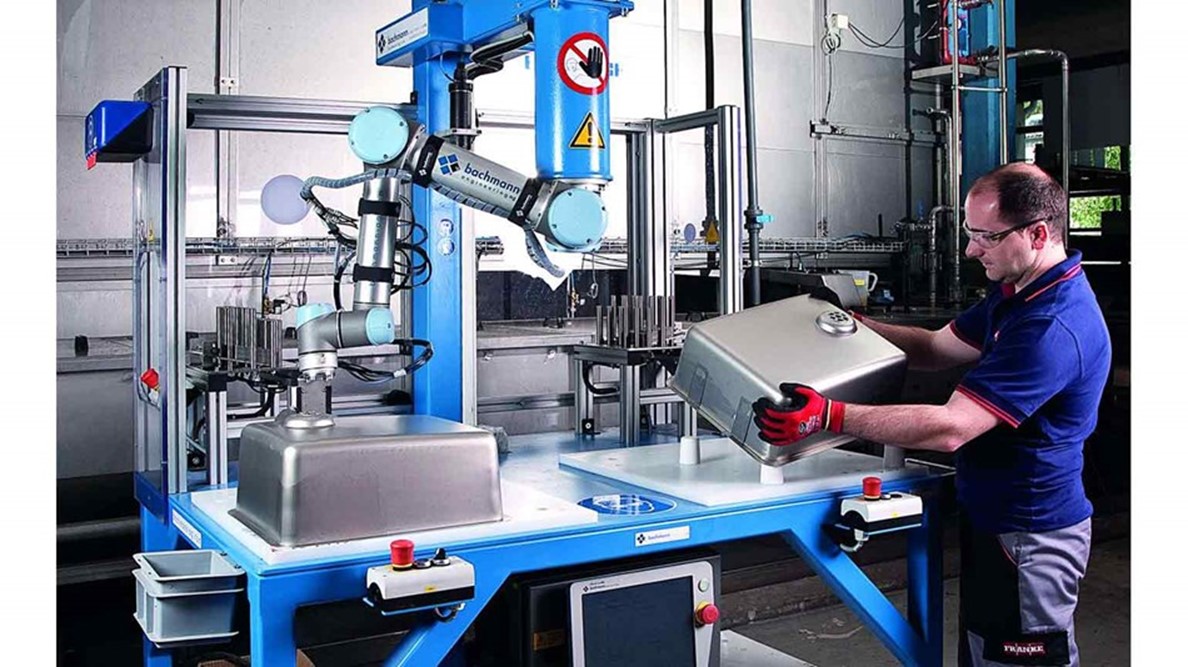
Применение датчиков и сенсоров в промышленной автоматизации
Датчики и сенсоры играют ключевую роль в промышленной автоматизации, обеспечивая высокую точность и эффективность процессов. Эти устройства позволяют в реальном времени измерять физические параметры, такие как температура, давление, влажность и движение, передавая данные в систему управления. Применение сенсоров способствует повышению производительности, снижению затрат и улучшению качества продукции, делая производство более гибким и безопасным.
Как датчики и сенсоры помогают улучшить управление процессами
Датчики и сенсоры в промышленной автоматизации — это неотъемлемая часть современных производственных систем. Они обеспечивают непрерывный мониторинг критических параметров и мгновенную передачу данных в систему управления, что позволяет операторам принимать решения на основе актуальной информации. Благодаря этим устройствам, процессы могут быть контролируемыми и оптимизированными в реальном времени, что способствует значительному улучшению производительности и снижению вероятности ошибок.
Преимущества использования датчиков и сенсоров:
- Повышение точности и стабильности. Современные сенсоры обладают высокой точностью измерений, что способствует стабилизации производственных процессов.
- Снижение затрат и ошибок. Системы, оснащённые датчиками, позволяют заранее выявлять неисправности или отклонения в процессе, минимизируя простой оборудования и связанные с этим финансовые потери.
- Обеспечение безопасности. Многие сенсоры используются для мониторинга состояния оборудования, предотвращая аварийные ситуации или выход из строя критически важных компонентов.
- Автоматизация процессов. Датчики позволяют интегрировать автоматические системы управления, которые могут регулировать параметры без участия человека, повышая оперативность реакции на изменения в процессе.
Применение в различных отраслях
Датчики и сенсоры находят широкое применение в разных отраслях промышленности, таких как:
- Пищевая промышленность — сенсоры контроля температуры и влажности в процессе хранения и переработки продуктов.
- Химическая промышленность — датчики давления и уровня для безопасного контроля химических реакций.
- Автомобильная индустрия — сенсоры для контроля качества сборки и функциональности деталей.
Внедрение таких технологий не только улучшает контроль за процессами, но и открывает новые возможности для инноваций и оптимизации, что важно для успешной конкуренции на рынке.
Типы датчиков, используемых в промышленной автоматизации
В промышленной автоматизации используются различные типы датчиков, каждый из которых выполняет свою специфическую функцию, обеспечивая точность и эффективность управления процессами. Один из самых распространённых типов — это датчики температуры, которые необходимы для контроля температурных режимов в процессе производства. Такие устройства используются в химических реакциях, отопительных системах, а также в устройствах, которые требуют поддержания постоянной температуры для качественного функционирования.
Датчики давления также играют важную роль, особенно в тех сферах, где требуется контролировать давление в трубопроводах и различных системах. Эти сенсоры помогают предотвращать аварийные ситуации, такие как перегрузка оборудования или его повреждения, что повышает безопасность и эффективность работы.
Кроме того, существуют датчики уровня, которые предназначены для контроля уровня жидкости или газа в резервуарах и трубопроводах. Они обеспечивают автоматическую регулировку процесса, гарантируя, что уровень материалов остаётся в допустимых пределах, что особенно важно для таких отраслей, как нефтехимия или водоснабжение.
Для контроля движения и положения объектов используются датчики движения и положения. Эти устройства могут автоматически регулировать работу роботов на сборочных линиях или обеспечивать точную позицию деталей в производственных процессах, значительно улучшая скорость и точность операций.
Как интегрировать датчики в систему управления оборудованием
Интеграция датчиков в систему управления оборудованием является важным этапом для повышения эффективности и безопасности производственных процессов. Этот процесс включает несколько ключевых этапов: выбор подходящих сенсоров, их подключение к системе управления и настройка для получения точных данных в реальном времени. Правильная интеграция позволяет не только повысить производительность, но и улучшить качество продукции, минимизируя риски ошибок и сбоев.
Первым шагом в интеграции является выбор датчиков, которые соответствуют требованиям конкретного производства. Необходимо учитывать такие факторы, как рабочие условия, тип измеряемого параметра и точность показаний. Например, для контроля температуры на производственных линиях лучше использовать термопары, а для измерения уровня жидкостей — ультразвуковые датчики.
После выбора сенсоров их подключение к системе управления осуществляется через соответствующие интерфейсы и протоколы связи. Это могут быть аналоговые или цифровые выходы, которые передают данные на контроллеры или системы мониторинга. Важно обеспечить правильное калибрование датчиков для точности измерений, а также интегрировать их с программным обеспечением, которое будет обрабатывать и анализировать полученные данные.
Кроме того, для эффективного управления системой датчиков важно настроить алгоритмы автоматической реакции. Например, в случае отклонения показателей от нормы, система должна быть настроена на автоматическое изменение параметров работы оборудования или на подачу тревожного сигнала оператору. Это позволяет предотвратить аварийные ситуации и минимизировать влияние человеческого фактора.
Настройка и калибровка датчиков для надежной работы
Настройка и калибровка датчиков — это критически важные процессы, которые определяют точность измерений и надежность работы всей системы. Неправильно откалиброванные датчики могут привести к ошибочным данным, что, в свою очередь, приведет к сбоям в производственном процессе, повышенному расходу материалов или даже аварийным ситуациям. Поэтому регулярная калибровка сенсоров является неотъемлемой частью их эксплуатации в промышленности.
Для правильной калибровки необходимо учитывать особенности каждого типа датчика. Процесс обычно начинается с проверки их точности в условиях, близких к рабочим. Например, при калибровке температурных датчиков используется специальное оборудование, которое позволяет сравнить показания датчика с эталонным источником температуры. Важно провести эту процедуру при различных рабочих температурах и давлениях, чтобы убедиться в стабильности показаний.
Кроме того, настройка датчиков требует настройки их откликов на изменения внешней среды. Например, в случае сенсоров давления нужно учитывать такие факторы, как изменение внешнего давления и температура окружающей среды, которые могут повлиять на точность показаний. Все эти параметры необходимо ввести в систему управления для обеспечения корректной работы и максимальной точности данных.
Регулярная проверка и калибровка датчиков гарантирует их долговечность и стабильную работу на протяжении всего срока службы. Это не только минимизирует риски возникновения производственных сбоев, но и способствует экономии на ремонте оборудования и повышению общей безопасности на предприятии.